What is Porosity in Welding: Essential Tips for Getting Flawless Welds
What is Porosity in Welding: Essential Tips for Getting Flawless Welds
Blog Article
Porosity in Welding: Identifying Common Issues and Implementing Ideal Practices for Prevention
Porosity in welding is a pervasive issue that typically goes undetected till it creates substantial troubles with the integrity of welds. In this discussion, we will explore the essential elements contributing to porosity formation, examine its harmful impacts on weld performance, and go over the finest methods that can be embraced to lessen porosity incident in welding procedures.
Typical Reasons For Porosity
One more constant perpetrator behind porosity is the presence of impurities externally of the base metal, such as oil, oil, or corrosion. When these contaminants are not properly removed prior to welding, they can evaporate and come to be trapped in the weld, causing defects. In addition, using filthy or wet filler materials can present contaminations into the weld, adding to porosity concerns. To reduce these typical root causes of porosity, extensive cleansing of base steels, proper shielding gas choice, and adherence to optimum welding parameters are vital techniques in attaining high-quality, porosity-free welds.
Impact of Porosity on Weld Quality

The visibility of porosity in welding can substantially compromise the architectural stability and mechanical residential or commercial properties of bonded joints. Porosity creates gaps within the weld metal, damaging its general strength and load-bearing capability.
Welds with high porosity degrees tend to exhibit lower effect stamina and minimized capacity to flaw plastically prior to fracturing. Porosity can impede the weld's ability to efficiently transfer forces, leading to premature weld failure and prospective security dangers in important frameworks.
Ideal Practices for Porosity Avoidance
To enhance the structural integrity and quality of welded joints, what specific measures can be implemented to minimize the occurrence of porosity during the welding procedure? Porosity prevention in welding is important to guarantee the stability and strength of the final weld. One reliable technique appertains cleaning of the base metal, removing any kind of impurities such as rust, oil, paint, or moisture that might bring about gas entrapment. Making certain that the welding devices is in good problem, with clean consumables and suitable gas circulation prices, can also helpful site significantly lower porosity. In addition, preserving a stable arc and regulating the welding specifications, such as voltage, current, and take a trip speed, aids produce a consistent weld swimming pool that reduces the threat of gas entrapment. Utilizing the correct welding strategy for the particular product being welded, such as readjusting the welding angle and gun placement, can additionally prevent porosity. Normal evaluation of welds and prompt remediation of any kind of issues recognized during the welding procedure are essential methods to stop porosity and generate top quality welds.
Importance of Proper Welding Methods
Carrying out appropriate welding strategies is extremely important in ensuring the structural integrity and quality of welded joints, building on the foundation of effective porosity avoidance measures. Welding strategies straight influence the total toughness and longevity of the bonded framework. One crucial element of Going Here appropriate welding methods is maintaining the correct heat input. Too much warm can cause enhanced porosity due to the entrapment of gases in the weld pool. Alternatively, not enough warm may result in insufficient blend, producing potential weak points in the joint. In addition, utilizing the suitable welding parameters, such as voltage, existing, and take a trip speed, is crucial for attaining sound welds with minimal porosity.
Additionally, the selection of welding process, whether it be MIG, TIG, or stick welding, need to align with the certain requirements of the job to make certain optimal outcomes. Correct cleaning and prep work of the base metal, along with selecting the ideal filler product, are also necessary parts of skilled welding strategies. By adhering to these best methods, welders can decrease the risk of porosity formation and create high-grade, structurally sound welds.
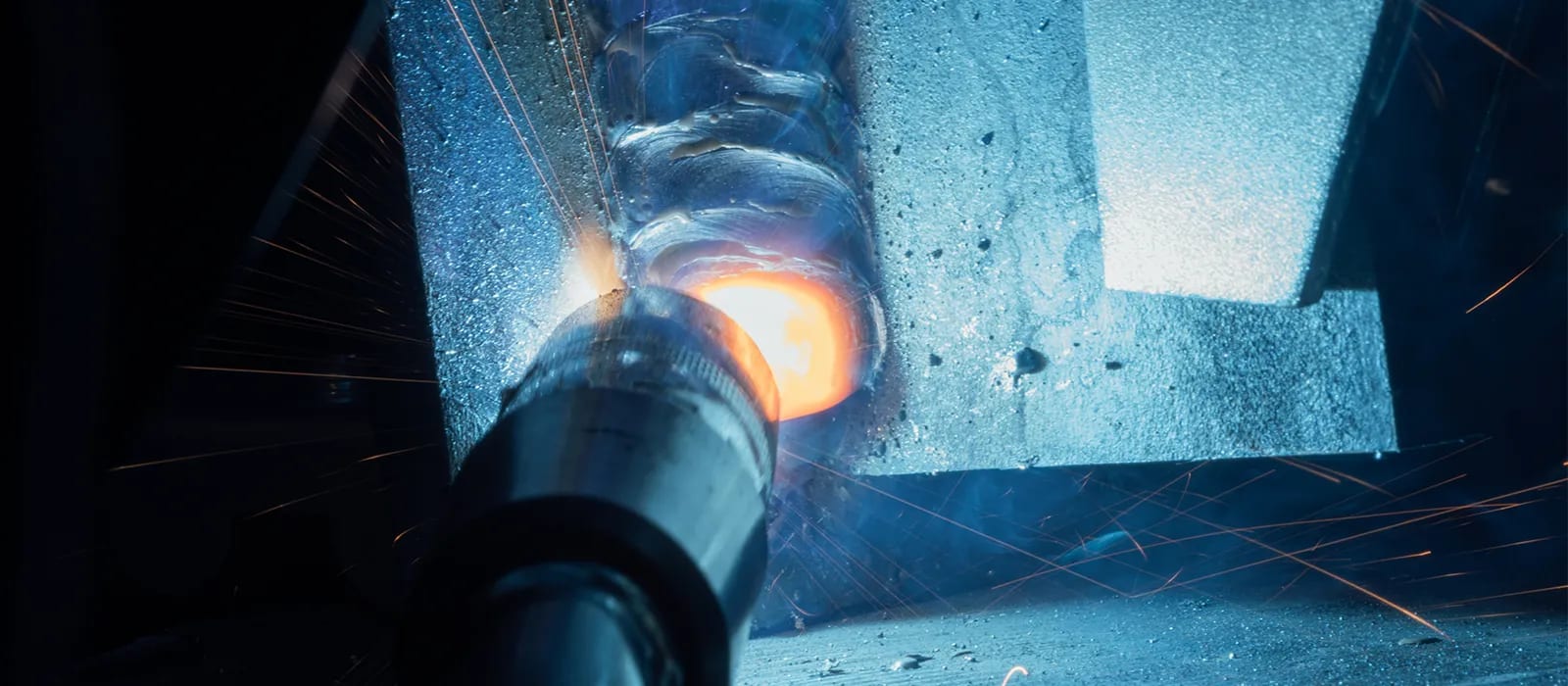
Testing and Quality Control Steps
Testing treatments are necessary to find and stop porosity in welding, guaranteeing the strength and durability of the last product. Non-destructive testing approaches such as ultrasonic testing, radiographic testing, and aesthetic evaluation are typically used to determine potential issues like porosity.
Carrying out pre-weld and post-weld examinations is likewise critical in preserving top quality control requirements. Pre-weld examinations involve confirming the products, equipment settings, and sanitation of the workspace to avoid contamination. Post-weld evaluations, on the various other hand, analyze the final weld for any type of flaws, including porosity, and confirm that it satisfies defined criteria. Executing a detailed top quality control strategy that includes extensive screening treatments and inspections is critical to decreasing porosity problems and making certain the total quality of welded joints.
Conclusion
Finally, porosity in welding can be a common concern that influences the top quality of welds. By determining the common causes of porosity and applying ideal methods for prevention, such as proper welding strategies and screening steps, welders can guarantee high top quality and trusted welds. It is vital to focus on prevention approaches to lessen the occurrence of porosity and keep the recommended you read stability of welded frameworks.
Report this page